Procure-to-Pay (P2P) is a critical process in managing a company’s procurement activities, ensuring seamless operations from purchasing to payment. Being proficient in all relevant SAP Transaction Codes (T-codes) not only streamlines workflows but also enhances accuracy and compliance within the organization. This guide provides the most commonly used SAP T-codes involved in the P2P process with complete explanations and practical examples to help you understand better.
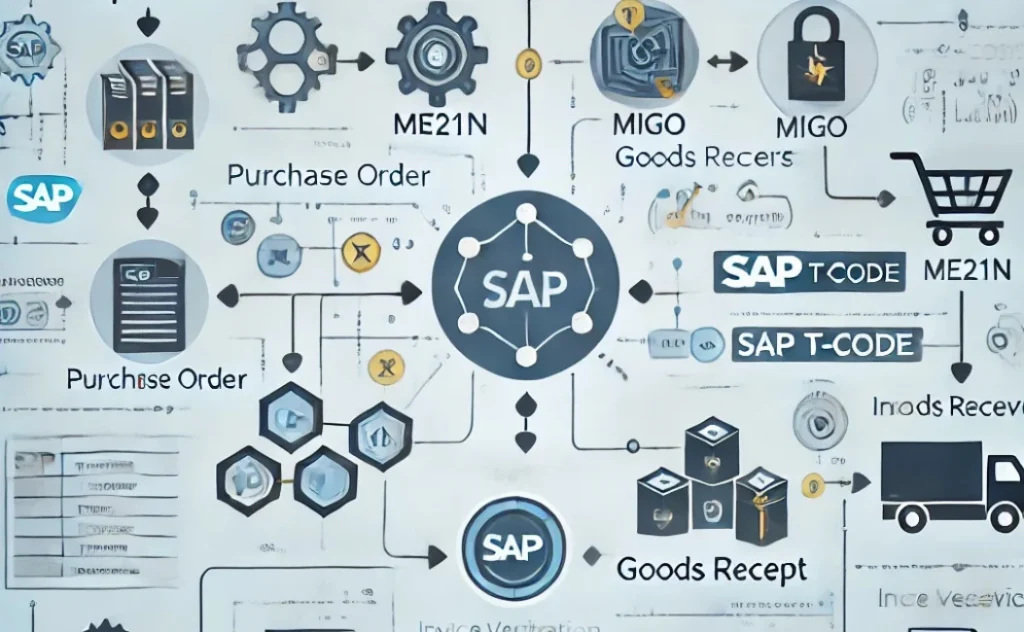
Vendor and Master Data Management
Managing vendor information is the foundation of the P2P process. The following T-codes help create, modify, and display vendor master data.
1. XK01: Create Vendor Master
- Used to create a new vendor record, including general, company code, and purchasing organization data.
- Example: A procurement manager uses XK01 to add a new supplier who provides office supplies, entering details like the vendor’s address, payment terms, and contact information.
2. XK02: Change Vendor Master
- Used to modify existing vendor master data, such as updating the vendor’s address or changing payment terms.
- Example: If a vendor relocates their headquarters, XK02 allows you to update their address in the system.
3. XK03: Display Vendor Master
- Used for viewing vendor master data without making any changes.
- Example: A finance officer uses XK03 to review a vendor’s payment history before processing an invoice.
Purchase Requisitions (PR)
Purchase Requisitions initiate the procurement process by specifying the materials or services needed.
4. ME51N: Create Purchase Requisition
- Initiates the procurement process by defining the materials or services needed.
- Example: A department head uses ME51N to request new laptops for the IT team, specifying the quantity and required delivery date.
5. ME52N: Change Purchase Requisition
- Allows users to edit an already created purchase requisition, such as adjusting quantities or delivery dates.
- Example: After reviewing inventory levels, the purchasing officer adjusts the quantity of laptops in ME52N to match current needs.
6. ME53N: Display Purchase Requisition
- Used to view details of an existing purchase requisition.
- Example: A manager reviews the details of a purchase requisition in ME53N to ensure accuracy before approval.
Request for Quotation (RFQ) / Quotation
RFQs are formal requests sent to vendors to obtain price quotes for specified materials or services.
7. ME41: Create RFQ
- Creates a formal request to vendors for price quotes on specified materials or services.
- Example: The procurement team uses ME41 to request price quotations from multiple vendors for office chairs.
8. ME42: Change RFQ
- Modifies details of an existing RFQ, such as delivery dates or payment terms.
- Example: If a vendor requests an extension on the delivery date, ME42 allows the procurement officer to update the RFQ accordingly.
9. ME43: Display RFQ
- View an RFQ along with all associated data and vendor responses.
- Example: A procurement analyst reviews vendor responses to an RFQ in ME43 to compare pricing and delivery options.
Purchase Orders (PO)
Purchase Orders formalize the agreement between the company and the vendor, outlining the terms and conditions of the purchase.
10. ME21N: Create Purchase Order
- Converts a PR or RFQ into a legally binding purchase document for a vendor.
- Example: After selecting the best vendor from the RFQ responses, ME21N is used to create a purchase order for office chairs.
11. ME22N: Change Purchase Order
- Edits an existing PO, such as updating quantities, delivery dates, or pricing.
- Example: If the company decides to increase the order quantity, ME22N allows the purchasing officer to adjust the PO accordingly.
12. ME23N: Display Purchase Order
- Allows viewing PO details such as line items, price conditions, and delivery schedules.
- Example: A project manager uses ME23N to check the status and details of an active purchase order.
13. ME29N: Release Purchase Order
- Approves or releases POs that are subject to a release strategy (approval workflow).
- Example: A senior manager reviews and releases a high-value purchase order in ME29N, completing the approval process.
Outline Agreements (Contracts & Scheduling Agreements)
Outline agreements define long-term purchasing terms and delivery schedules with vendors.
14. ME31K: Create Contract
- Creates a long-term purchase agreement with fixed conditions over a certain period.
- Example: The procurement department uses ME31K to establish a one-year contract with a supplier for regular delivery of office supplies.
15. ME32K: Change Contract
- Updates existing contract terms.
- Example: If market prices change, ME32K allows adjustments to the contract pricing terms.
16. ME33K: Display Contract
- Views contract details including validity periods, target values, and release orders.
- Example: A compliance officer reviews contract terms in ME33K to ensure they are being met.
17. ME31L: Create Scheduling Agreement
- Creates a schedule for deliveries of materials at predetermined intervals.
- Example: ME31L is used to set up a bi-monthly delivery schedule for raw materials from a supplier.
18. ME32L: Change Scheduling Agreement
- Changes existing scheduling agreements.
- Example: Adjusting the delivery dates in a scheduling agreement to accommodate changes in production schedules.
19. ME33L: Display Scheduling Agreement
- Views the conditions and delivery schedules in a scheduling agreement.
- Example: A logistics coordinator checks the delivery schedules in ME33L to plan warehouse space accordingly.
Purchase Info Records and Source Lists
These T-codes manage vendor-material-specific purchasing information and approved vendor sources.
20. ME11: Create Purchase Info Record
- Maintains vendor-material specific purchasing information, such as pricing and lead times.
- Example: Creating an info record for a new type of printer ink from a specific vendor.
21. ME12: Change Purchase Info Record
- Updates existing info records.
- Example: Adjusting the lead time for printer ink delivery in ME12 based on vendor feedback.
22. ME13: Display Purchase Info Record
- Views vendor-material relationship details.
- Example: Reviewing the pricing and terms for printer ink in ME13 before placing an order.
23. ME01: Create Source List
- Defines approved vendors for a material and controls source determination.
- Example: Creating a source list in ME01 to ensure only authorized vendors supply specific components.
24. ME02: Change Source List
- Updates source list entries.
- Example: Adding a new vendor to the source list for a material in ME02.
25. ME03: Display Source List
- Displays which vendors are assigned to a particular material.
- Example: Checking the approved vendors for a material in ME03 before initiating a purchase.
Goods Receipt and Inventory Management
Managing the receipt of goods and maintaining accurate inventory records is crucial for the P2P process.
26. MIGO: Goods Movement (Receipt/Issue/Transfer)
- Records the receipt of goods from vendors against POs, as well as other inventory movements.
- Example: Using MIGO to log the receipt of a shipment of laptops, updating inventory levels accordingly.
27. MMBE: Stock Overview
- Checks the stock level of materials in different plants or storage locations.
- Example: An inventory manager uses MMBE to verify stock levels before approving a new purchase requisition.
Invoice Verification and Accounts Payable
Ensuring that vendor invoices are accurate and processing payments efficiently are key aspects of the P2P cycle.
28. MIRO: Enter Incoming Invoice
- Posts vendor invoices against POs or delivery notes, initiating the payment liability.
- Example: Entering an invoice from the office supplies vendor in MIRO to trigger the accounts payable process.
29. MRBR: Release Blocked Invoices
- Releases invoices that have been blocked due to variances in quantity or value.
- Example: Resolving discrepancies in an invoice and releasing it for payment using MRBR.
30. MR8M: Cancel Invoice Document
- Cancels or reverses an already posted invoice.
- Example: If an invoice was entered incorrectly, MR8M is used to cancel the document.
31. FBL1N: Vendor Line Item Display
- Displays open and cleared line items for a particular vendor account.
- Example: Reviewing outstanding payments to a vendor in FBL1N to manage cash flow.
32. FB60: Enter Vendor Invoice (without PO)
- Posts invoices directly in Accounts Payable if not linked to a PO.
- Example: Recording a miscellaneous expense invoice in FB60 that wasn’t preceded by a purchase order.
33. FB65: Enter Vendor Credit Memo
- Posts credit memos from vendors.
- Example: Recording a credit memo for returned goods in FB65 to adjust the accounts payable balance.
Payments
Processing payments to vendors can be automated or handled manually to ensure timely and accurate transactions.
34. F110: Automatic Payment Run
- Executes automatic vendor payment proposals, generating payment documents and bank transfer files.
- Example: Running F110 at month-end to process all due vendor payments automatically.
35. F-53: Post Outgoing Payments (Manual)
- Posts manual bank payments to vendors.
- Example: Manually processing a one-time payment to a vendor using F-53.
36. FBZP: Maintain Payment Program Configuration
- Configures payment methods, bank selection, and payment terms for automated payments.
- Example: Setting up new bank accounts and payment terms in FBZP to align with updated vendor agreements.
Reporting and Analytics
Effective reporting and analysis help in monitoring and optimizing the P2P process.
37. ME2L / ME2M / ME2N: Purchase Order Reports by Vendor/Material
- Analyzes purchase orders by vendor or material.
- Example: Using ME2L to generate a report of all purchase orders placed with a specific vendor over the past quarter.
38. ME80FN: General Analyses (Purchasing Documents)
- Provides a comprehensive analysis of various purchasing documents.
- Example: Running ME80FN to analyze trends in purchasing patterns and identify cost-saving opportunities.
39. ME6B: Vendor Evaluation
- Evaluates vendors based on criteria like price, quality, and delivery performance.
- Example: Assessing vendor performance in ME6B to determine eligibility for future contracts.
Final Thoughts
Understanding and effectively utilizing these SAP T-codes can significantly streamline your organization’s Procure-to-Pay process. By mastering each step—from vendor setup to payment processing and reporting—you can ensure a more efficient and transparent procurement workflow.
This guide serves as a valuable resource for individuals looking to navigate the SAP P2P process. By using these T-codes and following best practices, you can optimize your procurement activities, reduce errors, and foster stronger relationships with your vendors. Keep this guide handy as a reference to enhance your SAP P2P expertise and drive operational excellence within your organization.