Are you preparing for SAP MM (Materials Management) interview? To help you out, we complied list of 35+ most commonly asked SAP MM interview questions with detailed answers. Whether you are an experienced professional or a fresher preparing for an interview, understanding the key concepts and commonly asked questions can significantly boost your confidence and competence.
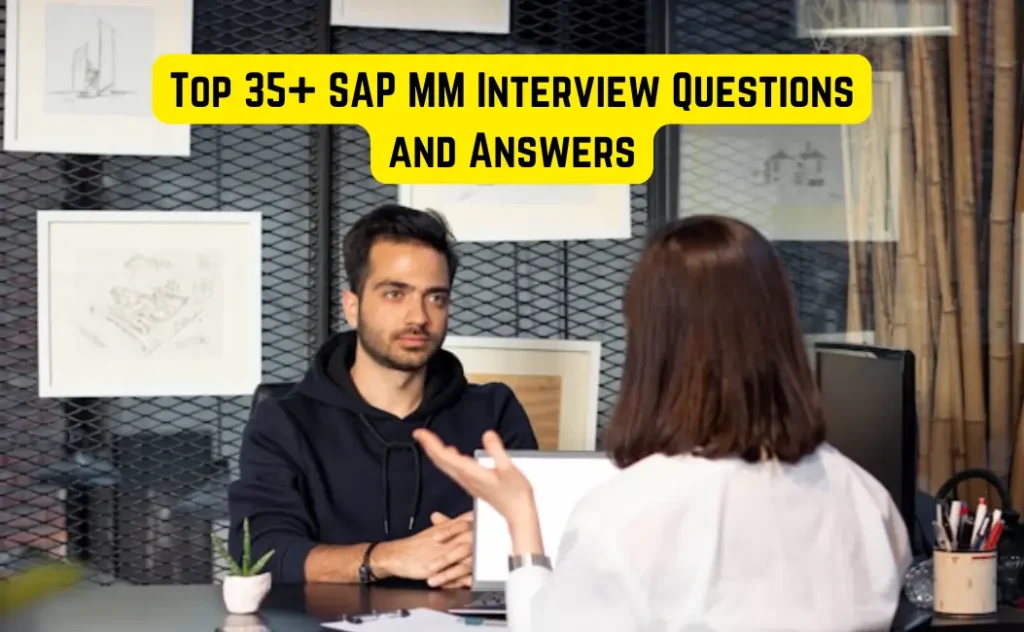
Top SAP MM interview questions and answers
- What is SAP MM, and what are its key functions?
- What are the organizational levels in SAP MM?
- Explain the procurement cycle in SAP MM.
- What is a material master record, and what are its key components?
- What is the difference between a purchase requisition and a purchase order?
- What is a valuation class in SAP MM?
- What is the purpose of a goods receipt in SAP MM?
- Explain the concept of split valuation.
- What is the purpose of a purchase info record?
- What is the difference between planned and unplanned goods movements?
- What is MRP in SAP MM, and how does it work?
- What is the difference between stock transfer and transfer posting?
- Explain the subcontracting process in SAP MM.
- What is the role of a source list in SAP MM?
- What are the types of stock in SAP MM?
- What is invoice verification in SAP MM?
- What is batch management in SAP MM?
- What are price control methods in SAP MM?
- What is the difference between a framework order and a standard PO?
- What is the role of Material Requirement Planning (MRP) in SAP MM?
- Can you explain the concept of consignment stock in SAP MM?
- What is a purchasing info record, and why is it important?
- Describe how you would handle a situation where received goods do not match the purchase order quantity.
- What are movement types in SAP MM?
- Explain how batch management works in SAP MM.
- What is split valuation in SAP MM?
- How do you create a purchase requisition in SAP MM?
- What is invoice verification in SAP MM?
- What are special stocks in SAP MM?
- Explain how you would handle returns to vendors in SAP MM.
- What is an evaluation class in SAP MM?
- How does MRP work with safety stock levels?
- Describe how you would set up automatic account determination in SAP MM?
- What is an RFQ (Request for Quotation), and how does it fit into procurement?
- Can you explain how pricing conditions are maintained in SAP MM?
- How do you manage inventory levels effectively using SAP MM?
- What steps would you take if there were discrepancies during physical inventory counts?
- Explain how you would configure new storage locations within an organization?
- What is external services management (ESM) within SAP MM?
1. What is SAP MM, and what are its key functions?
Answer:
SAP MM (Materials Management) is a core module in SAP ERP that supports procurement and inventory management processes. Its key functions include:
- Procurement Process: Managing requisitions, purchase orders, and supplier evaluations.
- Inventory Management: Monitoring stock levels, goods receipt, and goods issue.
- Invoice Verification: Ensuring invoices match purchase orders and goods receipt.
- Master Data Management: Handling material master, vendor master, and purchasing info records.
- MRP (Material Requirement Planning): Automating stock replenishment based on demand.
SAP MM integrates with modules like SD (Sales and Distribution), PP (Production Planning), and FI (Financial Accounting), ensuring a seamless flow of information.
2. What are the organizational levels in SAP MM?
Answer: The organizational levels in SAP MM define the structure within which material management activities are carried out:
- Client: The highest hierarchical level in an SAP system.
- Company Code: Represents an independent accounting entity.
- Plant: Represents a location where goods are manufactured or stored.
- Storage Location: A specific place within a plant to store materials.
- Purchase Organization: Handles procurement and negotiation with vendors.
- Purchase Group: A group of buyers responsible for specific procurement activities.
3. Explain the procurement cycle in SAP MM.
Answer: The procurement cycle in SAP MM involves the following steps:
- Requirement Determination: Creating purchase requisitions based on MRP or manually.
- Source Determination: Identifying suitable vendors using a source list or RFQ (Request for Quotation).
- Vendor Selection: Evaluating and selecting vendors.
- Purchase Order Processing: Converting purchase requisitions into purchase orders.
- Goods Receipt: Receiving and inspecting goods, updating stock levels.
- Invoice Verification: Matching the invoice with the purchase order and goods receipt.
- Payment Processing: Settling payment to vendors.
4. What is a material master record, and what are its key components?
Answer:
The material master record contains all information required to manage a material in SAP. It is divided into views based on functionality:
- Basic Data: General information like description, unit of measure.
- Purchasing: Details relevant to procurement like order unit and purchasing group.
- Accounting: Information for valuation, price determination.
- Storage: Data related to storage location and stock levels.
- MRP: Settings for planning, like reorder levels and lot sizing.
5. What is the difference between a purchase requisition and a purchase order?
Answer:
- Purchase Requisition (PR): An internal document requesting the purchase of materials or services. It is created before the vendor is identified and does not bind the company legally.
- Purchase Order (PO): A formal contract with the vendor that specifies materials, quantity, and prices. It is legally binding.
6. What is a valuation class in SAP MM?
Answer:
A valuation class is used in SAP MM to group materials with similar properties for valuation purposes. It determines which GL accounts will be posted during inventory transactions. For example:
- Raw materials might have one valuation class.
- Finished goods might have another.
7. What is the purpose of a goods receipt in SAP MM?
Answer: Goods receipt is the process of receiving materials or services into inventory. Its key purposes include:
- Updating stock levels in inventory.
- Verifying the quantity and quality of goods received against the purchase order.
- Triggering financial postings to record inventory value.
8. Explain the concept of split valuation.
Answer:
Split valuation allows you to manage materials with multiple valuation types within the same material master. For instance:
- A material may have different valuations based on origin (domestic/imported) or condition (new/used).
9. What is the purpose of a purchase info record?
Answer: A purchase info record links material and vendor data, including:
- Vendor-specific prices for a material.
- Delivery lead times.
- Last purchase order data.
- Discounts or special conditions.
10. What is the difference between planned and unplanned goods movements?
Answer:
- Planned Goods Movement: Triggered by a predefined process like a purchase order or stock transfer.
- Unplanned Goods Movement: Executed manually without a predefined reference, e.g., scrapping.
12. What is MRP in SAP MM, and how does it work?
Answer:
Material Requirements Planning (MRP) ensures that materials are available for production and procurement by calculating material needs based on demand and supply. MRP considers:
- Stock levels.
- Open purchase orders.
- Production schedules.
13. What is the difference between stock transfer and transfer posting?
Answer:
- Stock Transfer: Physical movement of materials between plants or storage locations.
- Transfer Posting: A logical change in material status (e.g., quality inspection stock to unrestricted stock).
14. Explain the subcontracting process in SAP MM.
Answer: In subcontracting, a company provides raw materials to a vendor who processes them into finished goods. Key steps:
- Create a subcontracting PO.
- Issue raw materials to the vendor.
- Receive finished goods from the vendor and perform goods receipt.
15. What is the role of a source list in SAP MM?
Answer: A source list specifies approved vendors for a material, ensuring compliance with procurement policies. It helps in:
- Vendor selection during purchase requisition.
- Avoiding unauthorized vendor purchases.
16. What are the types of stock in SAP MM?
Answer: Stock types include:
- Unrestricted Stock: Available for use.
- Quality Inspection Stock: Awaiting inspection.
- Blocked Stock: Not usable due to quality issues.
17. What is invoice verification in SAP MM?
Answer: Invoice verification matches the vendor’s invoice with the purchase order and goods receipt. It ensures:
- The correct amount is paid to the vendor.
- The accounting entries for inventory and accounts payable are accurate.
18. What is batch management in SAP MM?
Answer: Batch management tracks material quantities in batches, often used in industries requiring detailed tracking (e.g., pharmaceuticals). It ensures traceability and compliance.
19. What are price control methods in SAP MM?
Answer:
- Standard Price (S): Fixed value set in the material master.
- Moving Average Price (V): Average value recalculated after every transaction.
20. What is the difference between a framework order and a standard PO?
Answer:
- Framework Order: Long-term purchase agreement without fixed quantities.
- Standard PO: One-time procurement of specified quantities.
20. What is the role of Material Requirement Planning (MRP) in SAP MM?
Answer:
Material Requirement Planning (MRP) is a crucial function in SAP MM that ensures materials are available for production and products are available for delivery to customers. MRP helps in planning material requirements based on demand forecasts, production schedules, and inventory levels. It calculates the necessary quantities and timings for procurement or production, thereby optimizing inventory management.
The MRP process involves:
- Demand Management: Forecasting demand based on historical data.
- MRP Run: Executing the MRP run using transaction code MD01, which generates procurement proposals like purchase requisitions or planned orders based on the demand and supply situation.
- Lot Sizing: Determining the optimal order quantity to minimize costs while meeting demand.
- Exception Messages: Providing alerts for any discrepancies or issues in inventory levels, allowing for timely corrective actions.
21. Can you explain the concept of consignment stock in SAP MM?
Answer:
Consignment stock refers to materials that are stored at a customer’s premises but remain the property of the supplier until they are consumed. This arrangement allows companies to maintain inventory without incurring costs until the goods are used.
Key points about consignment stock include:
- Entry into Inventory: The stock is recorded in the inventory but is not valued until it is withdrawn for use.
- Invoice Processing: The supplier sends an invoice only after the customer consumes the stock, ensuring cash flow management for both parties.
- Transaction Codes: The creation of consignment stock can be done through standard purchase order processes, and specific transactions like ME21N can be used to manage these orders.
22. What is a purchasing info record, and why is it important?
Answer:
A purchasing info record is a vital piece of data that links a vendor with a material. It contains information such as pricing, delivery terms, and conditions specific to that vendor-material combination.
Importance of purchasing info records includes:
- Streamlined Procurement: Facilitates quicker purchasing processes by providing relevant vendor details directly linked to materials.
- Price History: Maintains historical pricing data, aiding in negotiations and budgeting.
- Automatic Price Determination: Ensures that prices are automatically fetched during the creation of purchase orders, reducing manual errors and time spent on data entry.
23. Describe how you would handle a situation where received goods do not match the purchase order quantity.
Answer: When received goods do not match the purchase order quantity, it is essential to follow a structured approach:
- Verification: Check the delivery note against the purchase order to confirm discrepancies.
- Communication with Vendor: Contact the vendor to resolve issues regarding short or excess deliveries.
- Goods Receipt Processing: In SAP, use transaction code MIGO to post a goods receipt for the quantity received. If there’s a shortfall, you can post only what was received while noting discrepancies.
- Adjustments: If necessary, create a follow-up document such as a debit memo for excess goods or initiate a return process for incorrect items using transaction code MB1B.
- Documentation: Ensure all communications and adjustments are documented for future reference and audits.
24. What are movement types in SAP MM?
Answer:
Movement types are three-digit codes in SAP that define various types of stock movements within inventory management. Each movement type specifies how materials are moved in or out of stock and affects inventory valuation accordingly.
Common movement types include:
- 101: Goods receipt from purchase order.
- 201: Goods issue for cost center consumption.
- 301: Stock transfer between storage locations within the same plant.
Each movement type has specific implications on inventory levels, accounting entries, and reporting within SAP MM.
25. Explain how batch management works in SAP MM.
Answer:
Batch management allows companies to manage inventory in batches rather than as individual units. This is particularly useful for industries where traceability of materials is critical (e.g., pharmaceuticals).
Key features of batch management include:
- Batch Creation: Batches can be created during goods receipt or production processes.
- Batch Characteristics: Each batch can have specific attributes (e.g., expiration dates, quality status) that need to be tracked throughout its lifecycle.
- Batch Selection: During sales orders or production orders, users can select specific batches based on criteria like shelf life or quality status using transaction codes like MB1C or MIGO.
26. What is split valuation in SAP MM?
Answer:
Split valuation allows organizations to manage different valuations of the same material based on certain criteria such as procurement type or origin. This is particularly useful when materials have different costs associated with them (e.g., locally sourced vs imported).
Key aspects include:
- Valuation Types: Different valuation types can be defined (e.g., standard price vs moving average price), enabling precise cost tracking.
- Integration with MRP: Split valuation integrates with MRP processes to ensure accurate planning based on different valuation scenarios.
27. How do you create a purchase requisition in SAP MM?
Answer: Creating a purchase requisition (PR) involves several steps:
- Navigate to transaction code ME51N.
- Enter relevant details including material number, quantity required, delivery date, and any specific notes regarding the request.
- Assign it to an appropriate purchasing group and specify whether it’s a stock or non-stock item.
- Save the requisition; it will then be routed through any defined approval processes before being converted into a purchase order if approved.
Purchase requisitions serve as internal documents that communicate needs from departments to purchasing teams.
28. What is invoice verification in SAP MM?
Answer: Invoice verification is a critical step in the procurement process where incoming invoices from vendors are checked against purchase orders and goods receipts before payment is processed.
The process involves:
- Three-Way Match: Ensuring that quantities and prices on the invoice match those on the purchase order and goods receipt.
- Transaction Code MIRO: Used to enter invoices into the system; discrepancies can trigger alerts for further investigation.
- Financial Impact: Accurate invoice verification ensures proper financial accounting by posting expenses against correct accounts while avoiding overpayments or duplicate payments.
29. What are special stocks in SAP MM?
Answer:
Special stocks refer to inventory categories that have specific ownership or usage conditions distinct from regular stock types. Common types include:
- Consignment Stock: Stock held at a customer’s location but owned by the supplier until consumed.
- Subcontracting Stock: Materials provided to vendors who manufacture products on behalf of another company.
- Project Stock: Inventory allocated specifically for project-related activities.
These stocks require special handling within SAP MM due to their unique nature concerning ownership and accounting practices.
30. Explain how you would handle returns to vendors in SAP MM.
Answer: Handling returns involves several steps:
- Identify items that need returning based on quality issues or incorrect deliveries.
- Use transaction code MIGO to initiate return processing by selecting “Return Delivery” option.
- Specify details such as quantity being returned and reference original documents (purchase order).
- Generate return delivery documents which can then be sent back to suppliers along with returned goods.
- Monitor credits received from vendors against returned items ensuring proper financial adjustments are made within accounts payable.
31. What is an evaluation class in SAP MM?
Answer: An evaluation class determines how materials are valuated within financial accounting processes in SAP MM. It links material master records with specific accounts used for posting transactions related to material movements and inventory changes.
Key functions include:
- Account Determination: It helps define which general ledger accounts will be affected during transactions like goods receipts or invoice postings.
- Integration with Valuation Area: Evaluation classes work alongside valuation areas (plant level vs company code level) ensuring accurate financial reporting across different organizational units.
32. How does MRP work with safety stock levels?
Answer: Safety stock acts as a buffer against uncertainties in demand and supply chain disruptions within MRP settings:
- Safety stock levels can be defined within material master records under MRP views.
- During MRP runs, safety stock levels influence procurement proposals; if actual stock falls below safety levels, additional orders may be generated automatically.
- Monitoring safety stock ensures that companies maintain service levels while minimizing excess inventory costs through effective planning strategies.
33. Describe how you would set up automatic account determination in SAP MM?
Answer: Setting up automatic account determination involves configuring settings within transaction code OBYC:
- Define valuation grouping codes that categorize materials based on their characteristics (e.g., raw materials vs finished goods).
- Assign account determination keys corresponding to different movement types ensuring accurate postings during transactions (e.g., goods receipts).
- Test configurations by executing typical transactions ensuring postings reflect correctly according to predefined rules.
This setup streamlines financial processes by automating entries linked directly to material movements without manual intervention.
34. What is an RFQ (Request for Quotation), and how does it fit into procurement?
Answer: An RFQ is a document sent out by buyers inviting suppliers to submit price quotes for specified goods or services:
- RFQs are created using transaction code ME41 where buyers specify details about required materials including quantities and delivery timelines.
- Suppliers respond with their quotations which can then be analyzed via transaction ME47 allowing buyers to compare offers before making decisions.
- Successful RFQ responses may lead directly into creating purchase orders once terms are agreed upon ensuring competitive pricing while maintaining supplier relationships.
35. Can you explain how pricing conditions are maintained in SAP MM?
Answer: Pricing conditions determine how prices are calculated during purchasing processes:
- Use transaction code MEK1 to create condition records specifying factors like price per unit based on vendor agreements or market rates.
- Conditions can also include discounts, surcharges, freight costs etc., allowing comprehensive pricing strategies tailored per vendor-material combinations.
- These records automatically apply during PO creation ensuring accuracy while reducing manual price entry errors significantly enhancing procurement efficiency.
36. How do you manage inventory levels effectively using SAP MM?
Answer: Effective inventory management involves several strategies facilitated through SAP MM functionalities:
- Implementing MRP settings ensures timely replenishment based on forecasted demands while maintaining safety stocks as buffers against variability.
- Regularly analyzing inventory reports helps identify slow-moving items allowing proactive decisions regarding promotions or discontinuation strategies.
- Utilizing physical inventory counts periodically reconciles discrepancies between system records versus actual counts ensuring data integrity across operations.
37. What steps would you take if there were discrepancies during physical inventory counts?
Answer: In case of discrepancies during physical counts:
- Reconcile differences by reviewing previous transactions leading up to counts checking for potential errors such as unposted receipts or incorrect adjustments made previously.
- Investigate reasons behind variances including thefts, damages etc., documenting findings thoroughly for audit trails if necessary.
3.Use transaction MI04/MI07 depending upon whether adjustments need posting against physical counts correcting discrepancies accordingly while maintaining transparency throughout processes involved ensuring accurate reporting post-counts completed successfully without impacting operational continuity adversely overall too much time spent resolving issues arising unexpectedly!
38.Explain how you would configure new storage locations within an organization?
Answer: Configuring new storage locations involves several steps:
- Navigate through SPRO menu selecting Logistics > Materials Management > Inventory Management > Storage Locations > Define Storage Locations where existing locations listed appear alongside options adding new ones easily!
- Enter relevant details such as name/location codes/description ensuring compliance with organizational standards established earlier before saving configurations made successfully!
- Test configurations by executing typical transactions involving movements between storage locations confirming seamless integration across all processes involved without disruptions occurring unexpectedly thereafter!
39.What is external services management (ESM) within SAP MM?
Answer:
External Services Management (ESM) facilitates managing services procured from external vendors effectively through dedicated functionalities integrated directly into core modules available already!
Key aspects include:
- Defining service specifications clearly outlining requirements expected from suppliers beforehand avoiding misunderstandings arising later down line causing delays unnecessarily!
- Creating service entry sheets capturing actual services rendered once completed allowing prompt invoicing/payment processing thereafter ensuring smooth cash flow management overall too!
- Monitoring performance metrics evaluating supplier efficiency regularly enabling continuous improvement initiatives identifying areas needing enhancement proactively addressing issues before they escalate further impacting operations negatively long term!
Learn More: Carrer Guidance
Top 31 Gallagher Interview Questions and Answers for Freshers
Top Free Power BI Courses with Certificates to Boost Your Data Analysis Skills
Databricks Interview Questions and Answers- Basic to Advanced
Kafka Interview Questions and Answers- Basic to Advanced
Chella Software interview questions with detailed answers