Just got your brand new Fleck 5600SXT installed, and you’re already seeing Error Code 0? Don’t Panic. This guide will walk you through what’s happening, why it’s happening, and how you can fix it—whether you’re a DIYer or just trying to understand before calling support.
What Is Fleck Error Code 0?
Error Code 0 stands for a Cam Sense Error. This occurs when the valve motor fails to reach the next regeneration position within 6 minutes. In simpler terms, your softener is trying to move into a new cycle, but something is stuck or misaligned inside the valve.
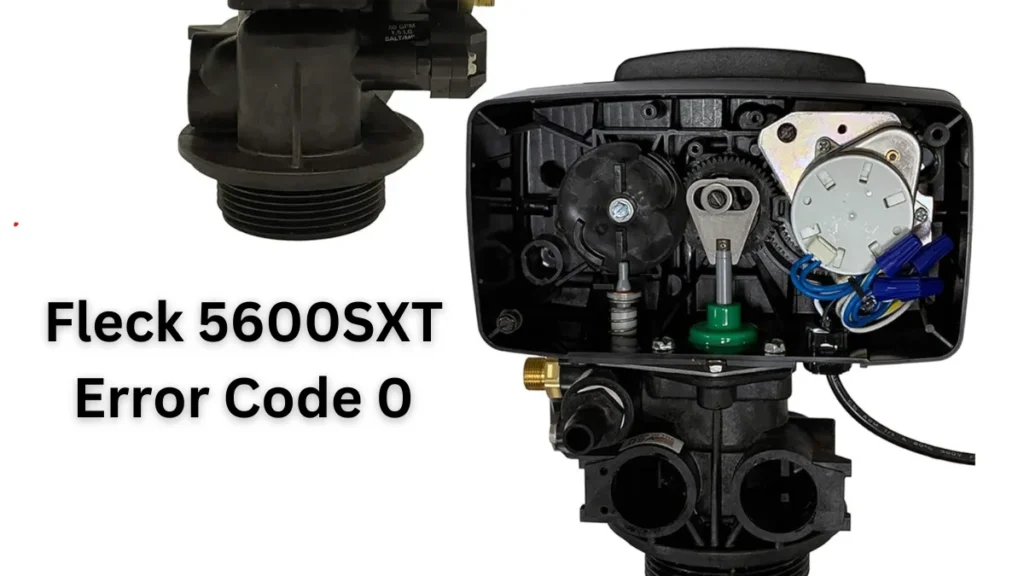
What Causes Error Code 0?
- Loose or unplugged cam switch
- Worn-out or misaligned motor or drive gears
- Piston stuck inside the valve body
- Poor internal assembly during installation
- Blockage or binding inside the control valve
Fleck 5600SXT Error Codes Overview
Here’s a quick look at all known Fleck 5600SXT error codes:
Error Code | Error Type | Meaning / Cause |
---|---|---|
0 | Cam Sense Error | Valve took too long (6+ minutes) to reach next regen position |
1 | Cycle Step Error | Unexpected cycle input; possibly wrong valve or system configuration |
2 | Regen Failure | System hasn’t regenerated in 99 days (or 7 days in Day-of-Week mode) |
3 | Memory Error | Control board memory failure |
UD | Upper Drive Sync | Power failure or programming change during valve movement (auto-recovers) |
Step-by-Step Fix for Fleck Error Code 0
Step 1: Power Cycle the Unit
- Unplug the power for 30 seconds.
- Plug it back in and watch the screen.
- If Error Code 0 appears again, continue to Step 2.
Step 2: Remove the Powerhead Cover
The powerhead sits on top of the valve body.
To remove the cover:
- Unplug the unit.
- Use a screwdriver to remove the two screws on the sides.
- Gently lift the cover off.
Inside, you’ll see:
- Drive motor
- Gear system
- Cam (yellow or red plastic disk)
- Micro-switches connected with wires
Step 3: Inspect the Cam, Gears, and Motor
Check the following:
- Cam gear: Is it cracked or misaligned?
- Gears: Are teeth worn or jammed?
- Motor: Try plugging in briefly—does it turn? Humming but not moving = jammed piston or motor failure.
- Wires & switches: Ensure the micro-switches are firmly connected to the circuit board.
Step 4: Manually Rotate the Cam and Check Movement
With power off:
- Gently rotate the cam disk by hand.
- If it resists, the piston may be stuck inside the valve.
- If it moves freely, the cam and gears are likely okay.
Step 5: Remove the Powerhead and Inspect the Piston
To check the piston:
- Disconnect wiring from the board and remove the motor.
- Remove drive yoke screw and mounting screws to lift off the full head.
- Underneath, you’ll see the piston rod inside the valve.
- Pull the piston assembly upward—it should slide out easily.
- Clean the piston, inspect for cracks or swelling.
- Lubricate it lightly with silicone grease and slide it back in.
Step 6: Reassemble the Head and Reset
- Carefully align the piston and drive gears.
- Replace the timer head on top of the valve.
- Ensure the main drive pin slots properly into the piston yoke.
- Reattach all screws and wiring.
- Plug the unit back in.
Step 7: Force a Manual Regeneration (Test)
- Press and hold the Extra Cycle button for 5 seconds.
- You should see the valve go to Backwash (BW).
- Press again to advance to each stage:
- BD (Brine Draw)
- RR (Rapid Rinse)
- BF (Brine Fill)
- If the unit moves through steps without stalling—success!
Bonus: How to Use Diagnostic Mode
You can check internal stats like flow rate and service hours:
- Press Up + Extra Cycle for 5 seconds while in service mode.
- View:
- FR = Flow Rate
- PF = Peak Flow
- HR = Hours in Service
- VU = Volume Used
- RC = Reserve Capacity
- SV = Software Version
Great for monitoring long-term behavior.
When to Call for Help
If:
- Motor doesn’t run at all
- Piston won’t budge or is cracked
- Gears are stripped
- Error reappears after manual regeneration
Then it’s time to call support:
Fleck / Pentair Tech Support: 800-279-9404 | [email protected] | Manual PDF
Final Thoughts
Fleck 5600SXT Error Code 0 is almost always a mechanical issue inside the powerhead or valve. Thanks to its modular design, you can often fix it yourself with some patience and care.
Whether you’re a homeowner, installer, or technician—this guide gives you everything you need to resolve the issue without hunting for manual guide.